Automatic production system of green forage sprouts
SIDRO
Industrial invention patent filed
PREFACE
The production of green forage sprouts in controlled environment has gained increased attention in recent years due to the shortage of agricultural land dedicated to food production and the negative consequences of climate change. However, the operational costs of the production systems used up to now and the limited availability of technologies are the main reasons for the limited adoption of this forage sprout production system. SERECO project represents the ideal solution for a comprehensive revision of the past techniques and strategies for the control of internal environment, irrigation and lighting, significantly enhancing automation, minimizing operator intervention, and, above all, reducing investment costs and the unit cost of the product.
WHEN TO USE IT
Sidro is suitable whenever it is desired to supplement the dry feed in livestock farming of cattle, buffalo, pigs, sheep, goats, and other smaller animals, with a portion of green and fresh substance not available for various reasons (unsuitable season, market availability, distance from pasture, high prices, etc.). The automatic SIDRO system produces the desired quantity and quality of green forage portion required for livestock 24 hours, 365 days a year, serving as a complementary feed to the dry forage and/or grains and/or pellets.
HOW IT IS MADE
SIDRO is essentially characterized by 5 integrated sections in a single automatic and robotic equipment: a seed weighing and soaking system, a seeding system, a cultivation system, a conveyor belt washing system and a forage cutting system. In addition to the above, SIDRO equipment always includes: the irrigation system, LED lighting system, wastewater collection system and a system for the treatment, recirculation and ozone sterilization of the same wastewater.
HOW IT WORKS
The system operates in a constant temperature and controlled humidity environment; therefore, for its installation, in addition to a supporting base usually made of concrete, is required a thermally insulated container that is conditioned and ventilated inside. Each day, a predetermined quantity of seed, determined through internal weighing system, is poured into the soaking tank where the seed is soaked in the presence of sterile water for a period that can vary from 2 to 20 hours. After soaking, the seed is transferred to the seeding tank by tilting the soaking tank. The seeding tank has a false bottom consisting of a conveyor belt suitable to sow different types of seeds. At the predefined time, the seeding system moves with both vertical and horizontal movements near the sowing belt. At this point, both the sowing belt and the seeding conveyor belt start simultaneously, the sowing process starts and, depending on the plant's capacity, it can last from 6 to approximately 30 minutes.
When the sowing is completed, the cultivation cycle begins, lasting about 7 days. During this period, the seed is regularly irrigated for short periods, followed by long pauses suitable to maintain the correct seed humidity in order to optimize germination and growth. A LED lighting system provides the right amount of light during the day, usually for a duration of 12 hours daily. The 7 cultivation belts are sown one per day, and the process is repeated for each one as described so far. On the seventh day, the germination and growth phase of the seedlings with only the nutrients contained in the seed is completed, so the unloading of the belt seeded seven days before is carried out.
The unloading phase begins at the time determined by the operator based on the needs and proceeds with the following steps: with the operator's consent on the touch screen, the cultivation belt and the forage removal conveyor belt are started, then the unloading of the forage, which is guided before falling into the cutting system, starts. The cutting system allows for the slicing of the forage carpet into strips of variable width at the discretion of the user and an undetermined length based on the fall onto the forage removal conveyor belt. Once the unloading and removal phase of the forage is completed, the brushing and washing phase of the just-unloaded cultivation belt begins, using sterile water. At this point, the unloaded and washed belt is ready to start the cycle again with a new sowing. The number of belts and the duration of the cultivation cycle allow for the daily production of the same quantity of product for 365 days a year.
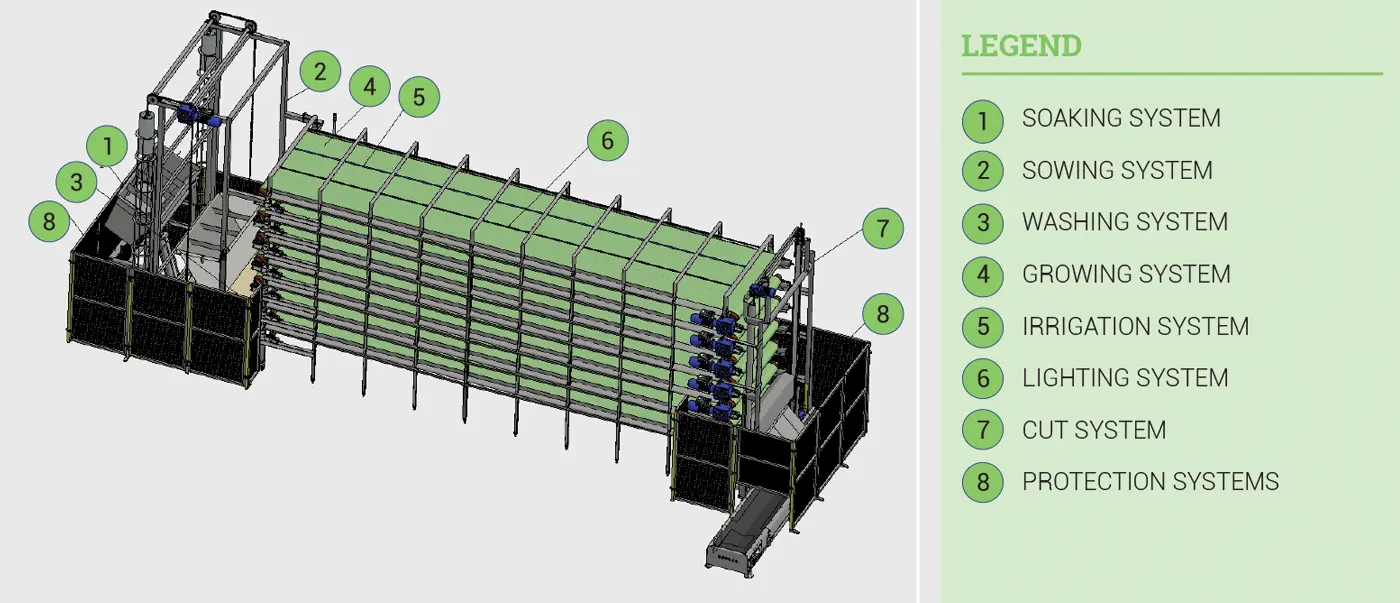